Hot Keywords:
Environmentally friendly UV water-based adhesive
Alcohol water gel

Feiyue New Material ·Our strength
Feiyue New Material ·Our strength

FEIYUE NEW MATERIAL · OUR STRENGTH

high-tech enterprise
● Is a collection of scientific research and development
● Production and sales and technical advice as one
● The company focuses on product development and innovation

Production process and formula
● Continuous research and development according to market demand
● Design and manufacture of new high-quality rubber rollers
● Increase the production process and formula of rubber roller

Service with heart
● Welcome new and old customers from all walks of life to negotiate and consult the relevant business
We will be excellent quality, sincere service
● Reasonable price for your service
20 years focus on the production of various rubber roller customization
Choose our 4 advantages

Feiyue New Material ·Products
Feiyue New Material ·Products

FEIYUE NEW MATERIAL · PRODUCTS CENTER
Product Center
Products
15 years experience in cots industry
A high-tech innovative enterprise specializing in providing high-quality rubber mixing for the rubber roller industry.

Feiyue New Material ·Service guarantee
Feiyue New Material ·Service guarantee

FEIYUE NEW MATERIAL · SERVICE PROTE
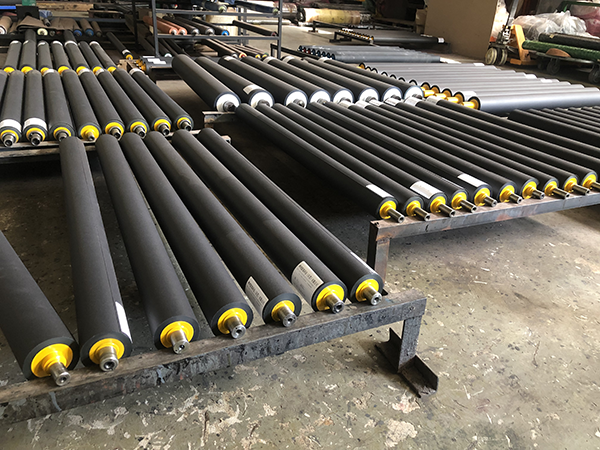
15 years experience in cots industry
15 years experience in rubber roller industry
Guangzhou Feiyue New Material Co., Ltd. is a high-tech innovative enterprise specializing in providing high-quality rubber mixing for rubber roller industry. The company always adheres to the brand new concept, advanced technology and innovative products to improve the quality of customers. With more than 15 years of experience in the rubber roller industry, the company's technicians have developed high-end UV special ink glue/water glue, UV dual-purpose ink glue/water glue, alcohol water roller glue, alcohol-free water roller glue, ordinary ink roller glue, environment-friendly water glue, environment-friendly ink glue, film-coated roller glue, rubber-plastic alloy, oil-filled rubber-plastic alloy and various industrial roller mixes in combination with Japanese technology, which are highly recognized by customers.
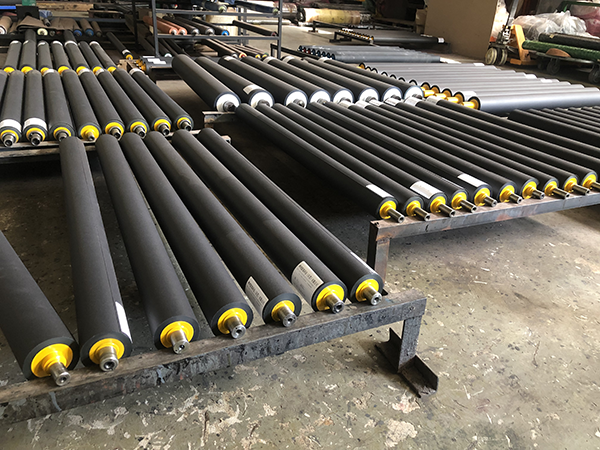
Strictly grasp the quality, guarantee the quality
Strict quality assurance
The company uses a variety of good raw materials, through professional production technology and strict product testing, quality assurance.
Hire professional and technical personnel, combined with the actual situation of the company, continuous improvement, innovation, tailor-made products for each customer.
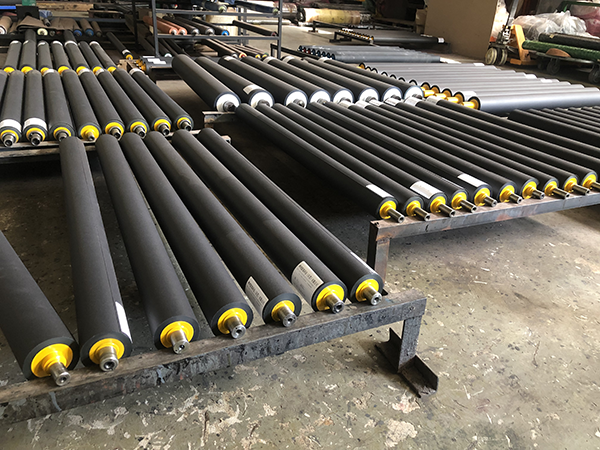
High production efficiency, fast shipment
High production efficiency, fast delivery
We have large PU automatic pouring machine, rubber mixing machine, internal mixer, grinding machine, computer numerical control lathe, milling machine and other professional equipment.
We have a professional technical team to improve production efficiency. At the same time, we have long-term cooperation with several logistics providers to ensure timely delivery.
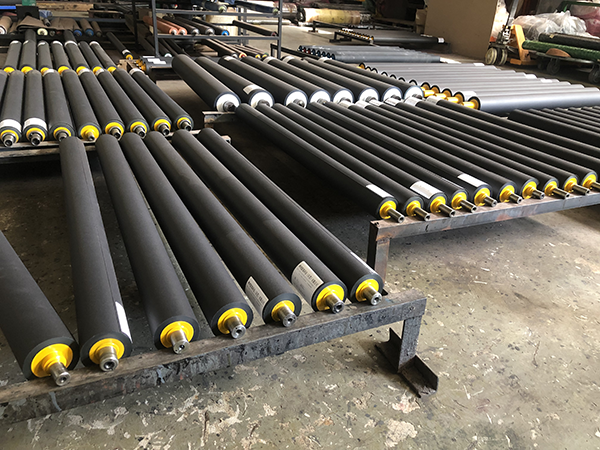
Perfect service system
Perfect service system
We have a professional service team to help you solve pre-sales, sales, after-sales and other issues. There are more online and offline customer service centers to quickly respond to customers' various questions, making you more worry-free.
Service Hotline: 13246826678 15818839509

Feiyue New Material ·Partners
Feiyue New Material ·Partners

FEIYUE NEW MATERIAL · PARTNER
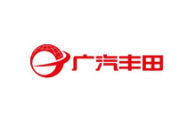
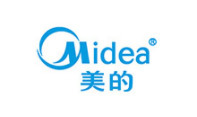
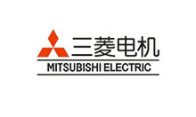
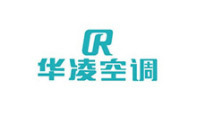
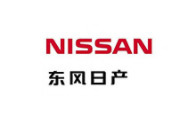
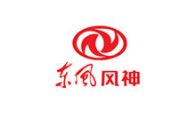
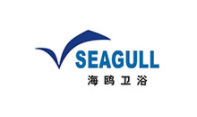
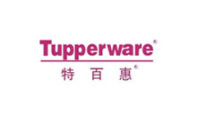
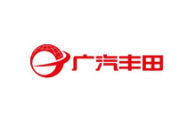
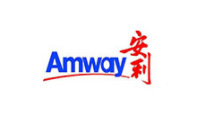
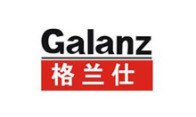
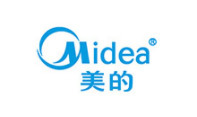
ABOUT US
About Feiyue New Material
Guangzhou Feiyue New Material Co., Ltd. is a high-tech innovative enterprise specializing in providing high-quality rubber compounds for the rubber roller industry. The technical staff has more than 15 years of experience in the rubber roller industry.It combines Japanese technology and unique processes to develop high-end UV special ink glue / water glue, UV dual-purpose ink glue / water glue, alcohol water roller glue, and alcohol free water. Roller glue, ordinary ink roller glue, environmentally friendly water glue, environmentally friendly ink glue, film-coated roller glue, rubber-plastic alloy, oil-extended rubber-plastic alloy and various industrial roller compounded rubbers are highly recognized by customers.
View Details +
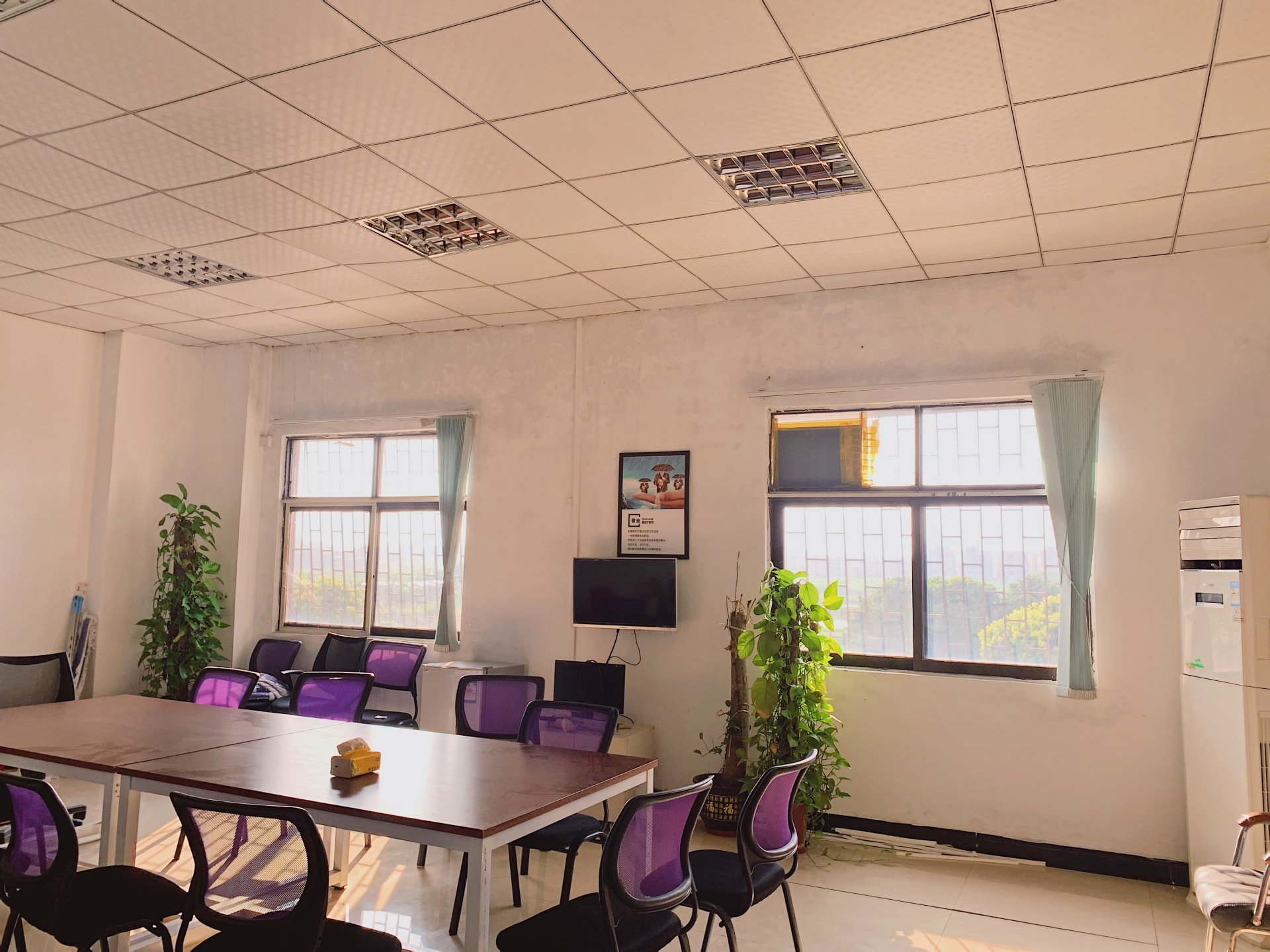
Work Environment
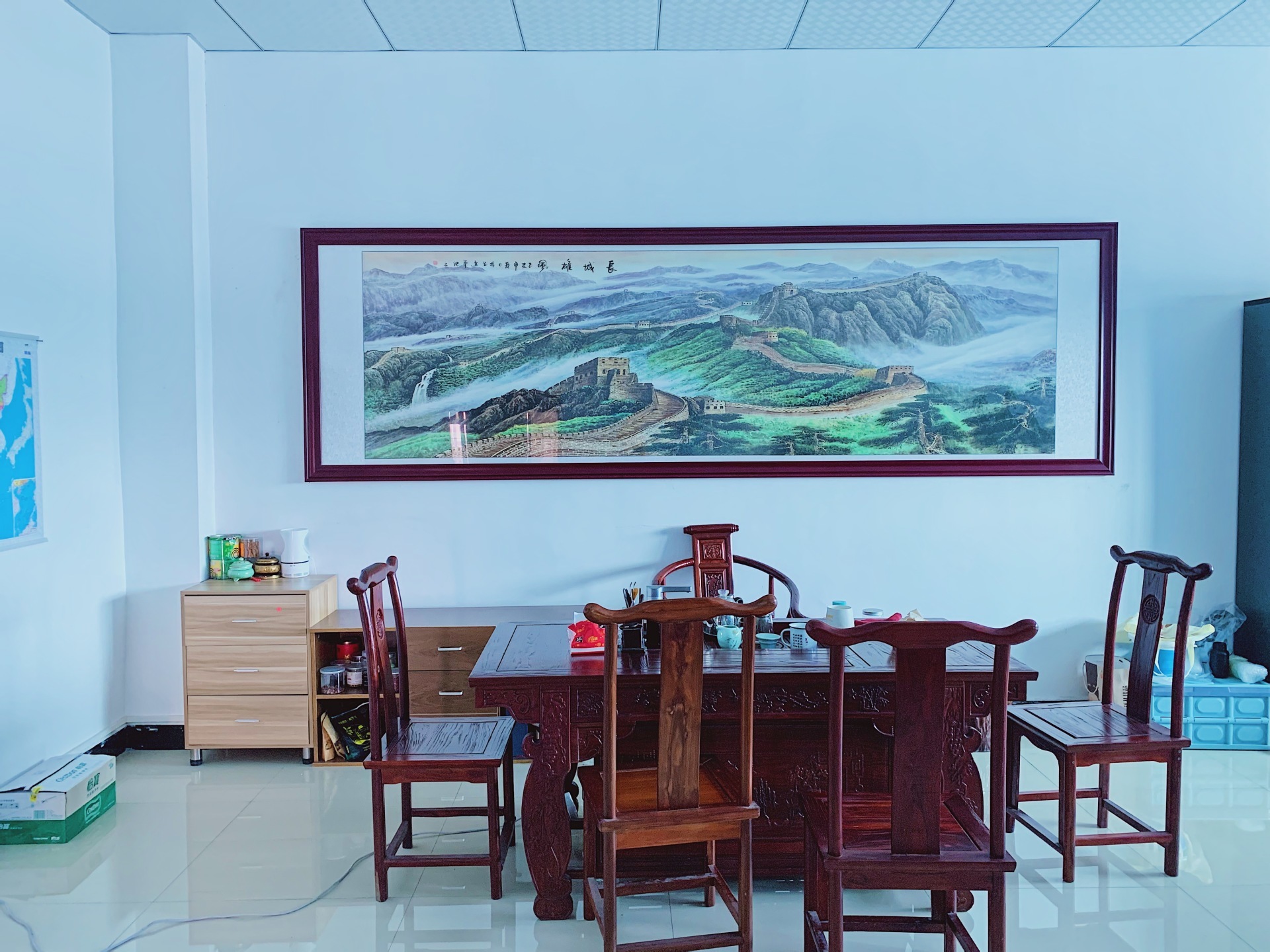
Work Environment2
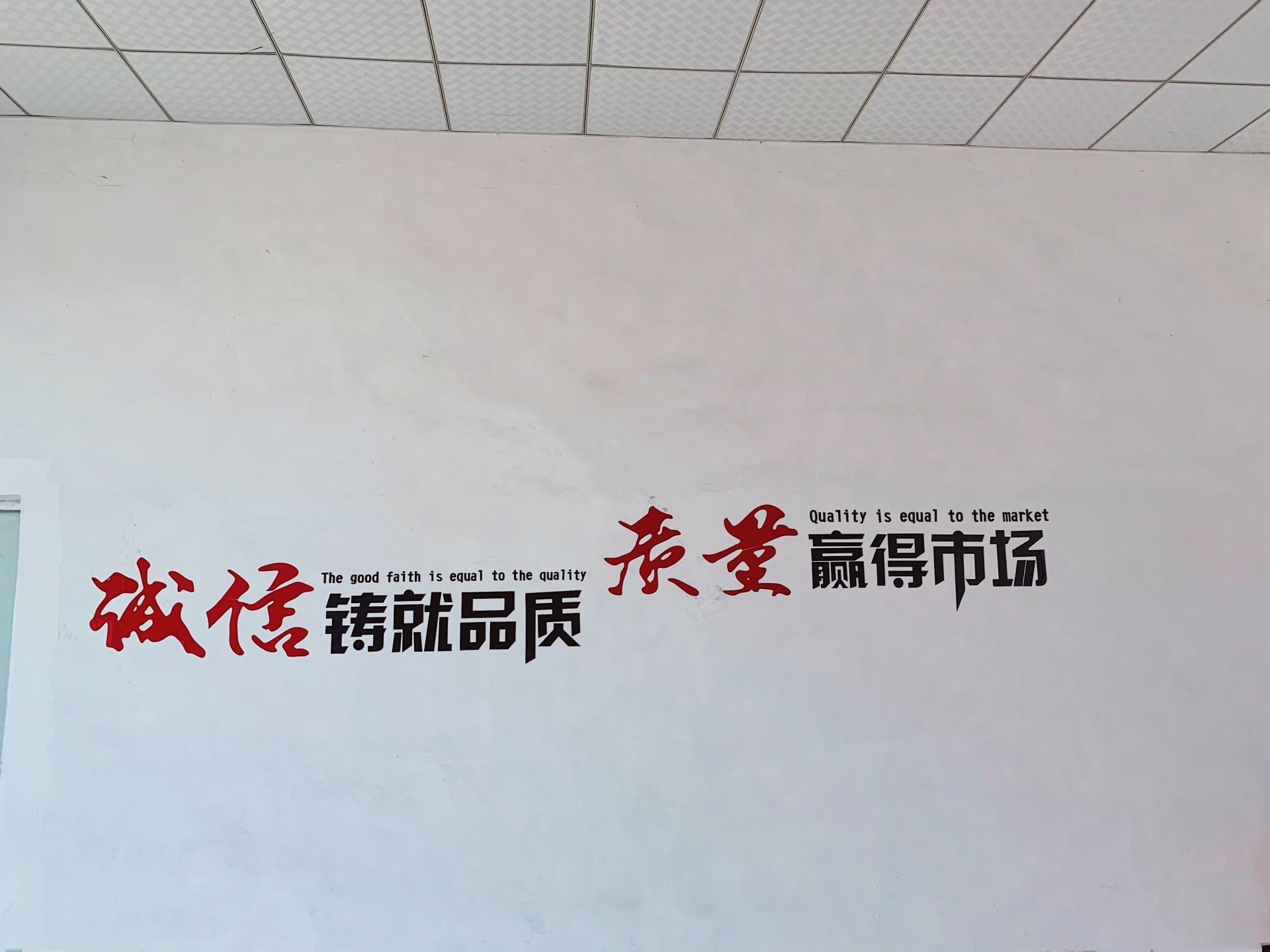
Work Environment3
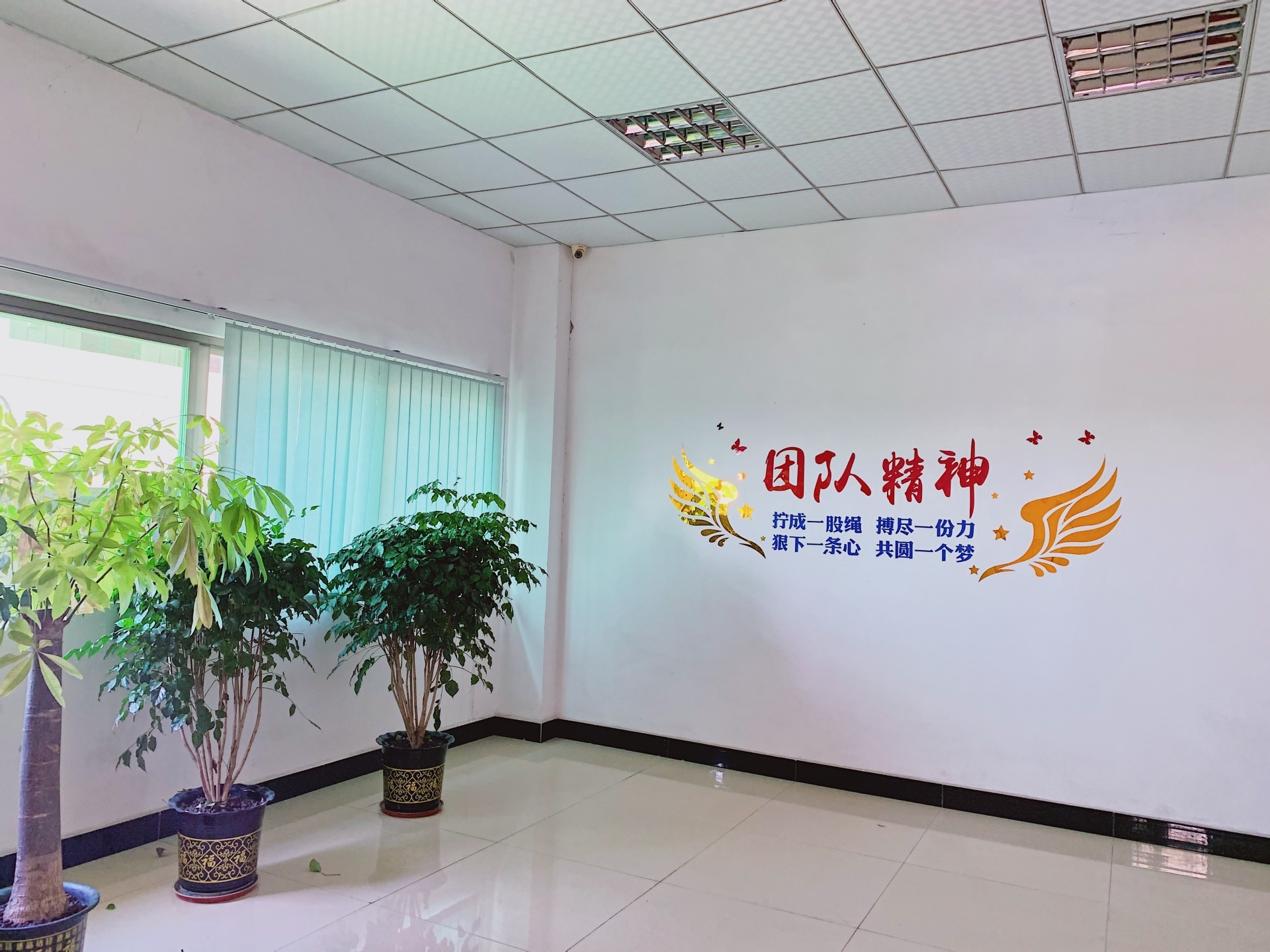
Work Environment 4
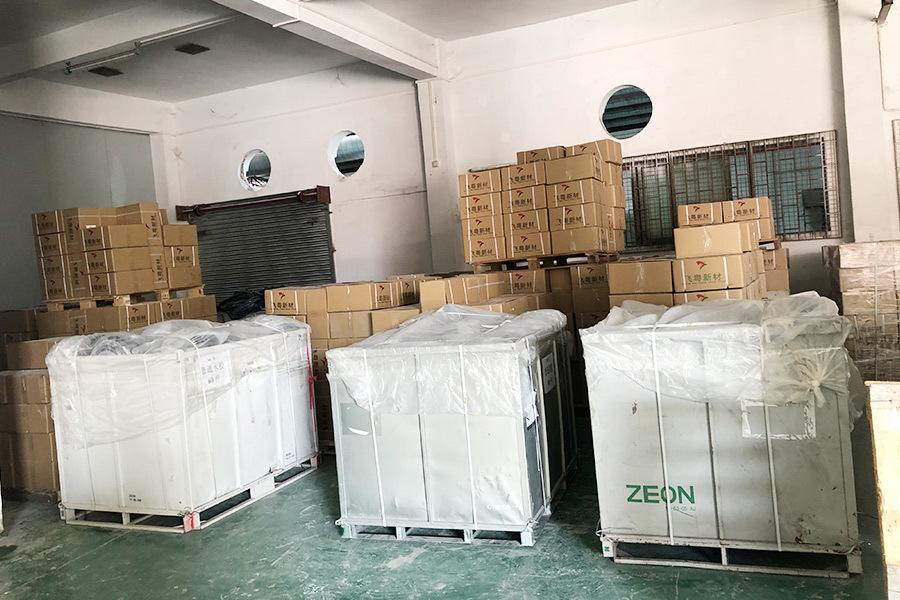
Factory environment 1
News
Supplier of compounded rubber: Factors affecting the compounding process
Release time :2022/07/08
View DetailsCommon Problem

1. The printing rubber roller mainly transmits ink on the offset printing machine. Therefore, when cleaning the stone rubber roller daily, it is essential to clean it thoroughly; otherwise, it will cause a smooth and hard film to form on the surface layer of the printing rubber roller due to oxidation with pigments and resins, affecting ink transfer. If it is not cleaned regularly, the surface of the printing rubber roller will become uneven over time, making it difficult to use. Therefore, when stopping the machine, the printing rubber roller should be cleaned and stored properly for future use.
2. In offset printing operations, the emulsification of ink caused by "too much water and too much ink" creates a hydrophilic base on the smooth printing rubber roller, leading to ink removal. The solution is to scrape off the emulsified ink, clean the ink-removing rubber roller with gasoline, and polish it with a 5% sodium hydroxide aqueous solution mixed with pumice powder. At the same time, the metal rollers (or hard rollers) should also be treated accordingly. Hard rollers can also be polished with fine water sand while being sprayed with water, taking care not to stay fixed in the same position, as this may damage the printing rubber roller. The fundamental solution is to control the pH value of the water tank liquid and maintain a good water-ink balance.
3. If the printing rubber roller has been used for too long and has aged, combined with the erosion of chemical agents, it may cause the rubber to shed "grains." Such printing rubber rollers are best not to be used again, as they severely affect the quality of the printed products.
4. To ensure that production and printing quality are not affected, there must be spare ink rollers, but do not store too many to avoid aging. The storage environment for printing rubber rollers should be the same as that for rubber blankets. Additionally, the printing rubber rollers should be placed straight at the shaft neck, and their surfaces should not touch each other or other items to prevent deformation.
5. Printing rubber rollers should not be stored near large electric motors or generators. The large amount of ozone produced by these devices can cause the surface of the printing rubber rollers to age and crack.
6. In cold weather, if the ink does not apply evenly, auxiliary materials can be added to the ink. It is prohibited to use infrared heaters or similar devices to bake the ink rubber rollers to prevent oxidation.

Rubber rollers are widely used in textile, papermaking, leather, packaging and other equipment for pressing rubber rollers, as well as in industries such as metallurgy, mining, printing, dyeing, chemical fiber, and papermaking for traction rubber rollers. They have excellent elasticity and mechanical strength, and good alkali resistance. Since the internal structure of newly cast rubber rollers is not yet stable, using them immediately can easily reduce their lifespan. Therefore, the maintenance of Shipa rubber rollers is very important. Below are the precautions to take during use:
1. Before Printing
Check for foreign objects between the rollers, ensure the rubber rollers are intact, and that the pressure between the rollers is uniform and consistent. Confirm normal conditions and clean thoroughly before proceeding with printing.
2. During Printing
Shipa rubber rollers should always maintain good contact during operation, with uniform and consistent force. Regardless of the width of the printed product, the entire rubber surface of the roller should be lubricated with ink oil; depending on the amount of ink accumulation between the rollers, the ink volume should be adjusted in a timely manner to ensure printing quality.
To prevent the ink from drying too quickly, which would reduce the viscosity of the rubber rollers and cause skin formation on the surface, the amount of drying oil added to the ink should be controlled to prevent issues with ink transfer and uneven ink application during operation.
3. After Printing
Timely separate the rollers from each other and from the printing plate to relieve pressure and prevent deformation of the rubber surface due to static pressure. Clean the residual ink from the surface of the rubber rollers promptly to prevent drying, which can lead to ink clumps, ink films, and dirt floating on the rubber surface (especially ink clumps on both ends of the nylon rollers), which can damage the smoothness of the rubber surface during operation, and in severe cases, cause pitting and flaking.
4. Cleaning the Rubber Rollers
Shipa rubber rollers must be cleaned with a special cleaning agent before and after printing to maintain a smooth surface for future use.
If cleaning is not done in a timely manner, ink can adhere to the micro-pores on the surface of the rubber rollers, trapping paper fibers and dirt. If the downtime is too long, the ink film can cause the contact surfaces of the two rollers to stick together, and when restarted, it can tear the rubber surface, rendering the rubber roller unusable.
Inadequate cleaning can lead to glazing, which reduces ink affinity and transfer capability, and can even cause ink removal issues. Glazing increases the hardness of the rubber roller surface, decreases elasticity, and accelerates wear, leading to pitting and cracking on the rubber surface, causing flaking and affecting printing quality.

Debugging and proper use
Regardless of the type or model of the printing machine, after the new equipment is installed, the printing rubber roller must first be installed by technicians and the lead machine. The height of the rubber roller must be adjusted reasonably, and it must be in close contact with the ink roller and the printing plate; both are indispensable. Those engaged in printing know that the height of the relief plate is 3.14mm, which is consistent with the height of the type, while the PS plate is relatively lower at 1.2mm, so when installing and adjusting the rubber roller, one must be aware of this. If it is a printed product with a background color, the rubber roller can be adjusted a little lower, with an error of ±0.5mm, so that the ink transferred from the ink roller to the printing rubber roller is more uniform, and the same effect is reflected on the printing plate, making the printed product pleasing to the eye. If not, phenomena such as ink streaks and ink paths will occur.
When printing text, the height of the rubber roller should be basically level with or slightly lower than the text plate, so that the printing rubber roller can gently rub against the printing plate, resulting in very clear and clean text printing. The wear surface of the rubber roller is small and not easily damaged, which can extend the service life of the printing plate. During adjustment, a rubber roller adjustment tool should be used. Before use, the printing plate should be removed, and the adjustment roller should be inserted and pulled out a few times to level it. The size of the ink dots on the adjustment roller will immediately be displayed, and the operator can determine the height of the printing rubber roller according to different printing needs, and then secure the top screw. This way, the height of the rubber roller will not change during high-speed printing.
If we lack patience when using the rubber roller and are eager to achieve results for convenience, the following situations may occur:
(A) The rubber roller may show surface damage, flaking, causing the text printing to be incomplete, unclear, or even resulting in smudging and jumping ink.
(B) The ink coverage on the text is uneven, and there may even be printed products with only text impressions but no ink color.
(C) If the rubber roller is adjusted too tightly against the ink transfer rubber roller, it may damage the printing rubber roller, causing economic losses and equipment accidents. In the technology of offset printing, the key is the control of the balance between the water path and the ink path, and the balance of water and ink relies on the rubber roller and ink roller, which are key components whose quality directly affects product quality. This is even more true for gravure, relief, and flexo printing.
General printing companies must maintain their equipment once a week, which includes the maintenance of the printing rubber roller. The maintenance methods are as follows:
1. After completing daily production operations, the rubber roller should be carefully cleaned and washed twice.
2. Cleaning the printing rubber roller must use designated chemical agents, such as industrial alcohol, and must not use corrosive solvents.
3. During holidays, the rubber roller should be removed to prevent deformation due to pressure.
4. For the protection of the surface of the printing rubber roller, it should be wrapped in newsprint and placed in a ventilated, dark place. In the working process, the printing rubber roller usually shows wear, holes, and other phenomena. If a new roller is replaced, the cost is too high and affects production progress.
Rubber repair agents can be used for repair. The repair process, taking rubber repair agents as an example:
1. Surface treatment: The area to be repaired should be roughened, cleaned, degreased, and dried.
2. Mixing the repair glue: Pour the curing agent B group of the rubber repair agent into the main agent A group and stir quickly until evenly mixed (A:B=1:1), then pour it onto the area to be repaired and smooth it out.
3. Curing: It can be used after curing at room temperature for 4-6 hours, and reaches maximum strength after 48 hours.